Are you aware that the chemical industry relies heavily on stainless steel for its equipment and infrastructure?
Imagine a scenario where a chemical plant requires materials that can withstand the corrosive effects of acids, alkalis, and other harsh chemicals. Stainless steel emerges as the go-to solution, offering exceptional resistance to corrosion and ensuring the longevity of critical components.
But what sets stainless steel apart in these challenging environments? Stay tuned to discover the unique properties of stainless steel that make it indispensable in the chemical industry, and how it continues to shape the landscape of chemical processing.
Key Takeaways
- Stainless steel is highly resistant to corrosion from highly corrosive substances, making it suitable for use in the chemical and petrochemical industries.
- It has impressive mechanical characteristics and can withstand aggressive conditions such as treated fluids and high temperatures.
- Stainless steel is commonly used in pressure vessels, process piping, platform accommodation, cable trays, subsea pipelines, tanks, pipes, pumps, and valves in the chemical and petrochemical industries.
- Different types of stainless steel, such as ferritic, austenitic, martensitic, duplex, and precipitation hardening, offer various properties and advantages for different applications in the industry.
What makes stainless steel the best choice for corrosive environments
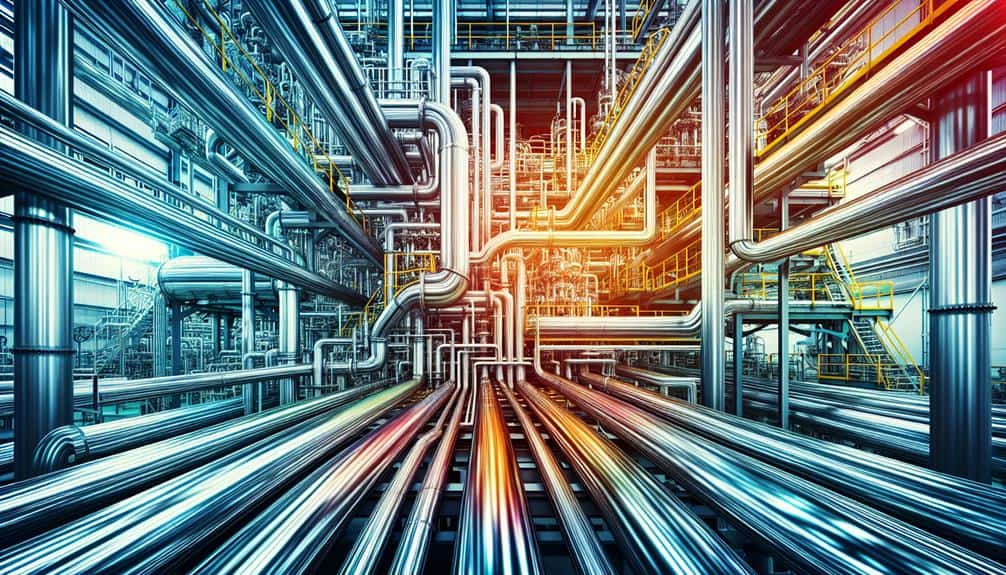
Stainless steel emerges as the optimum choice for corrosive environments due to its exceptional resistance to a wide range of chemicals, providing longevity and reliability in demanding industrial settings.
The advantages of stainless steel in corrosive environments are evident in its remarkable longevity. It offers a cost-effective solution due to its minimal maintenance requirements, reducing the overall lifecycle cost. The versatility of stainless steel is unparalleled, as it can be easily modified for various components and units, contributing to its cost-effectiveness in maintenance and repairs.
Its ability to withstand aggressive conditions, such as treated fluids and high temperatures, ensures its longevity in corrosive environments. Additionally, the high resistance to corrosion from highly corrosive substances makes stainless steel an ideal choice for applications in chemical and petrochemical industries.
The remarkable mechanical characteristics of stainless steel further enhance its suitability for withstanding aggressive conditions, making it the preferred material in corrosive environments.
5 types of stainless steel
When considering the types of stainless steel for your chemical or petrochemical application, you’ll encounter several distinct options.
Ferritic stainless steel, reliant on chromium, is suitable for thin sections and offers resistance to stress corrosion cracking.
Austenitic stainless steel, the most prevalent variety, provides enhanced corrosion resistance with added chromium and molybdenum.
Martensitic stainless steel, with higher carbon content, is hardened and tempered to deliver high strength and moderate corrosion resistance.
Duplex stainless steel, a blend of ferritic and austenitic microstructures, offers improved strength and resistance to stress corrosion cracking.
Lastly, precipitation hardening (PH) stainless steel, characterized by super-strong properties and a strong particle matrix, can be machined into intricate shapes to suit specific application requirements.
Ferritic
The ferritic type of stainless steel, based on chromium and known for its resistance to stress corrosion cracking, is widely utilized in various industrial applications. Ferritic stainless steels are magnetic and have good ductility, making them suitable for a wide range of applications.
These steels offer excellent corrosion resistance in many environments, including those containing chlorides and sulfurous acids. They find extensive use in automotive applications, architectural cladding, and kitchen equipment due to their attractive appearance and ease of fabrication.
The advantages of ferritic stainless steel lie in their high thermal conductivity, low thermal expansion, and good oxidation resistance at high temperatures. Their applications span from automotive exhaust systems to heat exchangers, making them a versatile and valuable material in the chemical industry.
Austenitic
Ferritic stainless steel, known for its resistance to stress corrosion cracking and magnetic properties, plays a vital role in various industrial applications.
Now we’ll focus on the characteristics of the austenitic type of stainless steel. Austenitic stainless steel, with its enhanced corrosion resistance due to added chromium and molybdenum, finds extensive applications in industries such as chemical, petrochemical, and pharmaceutical.
Its non-magnetic properties and excellent formability make it suitable for various structural and decorative applications. Compared to other types of stainless steel, austenitic steel offers superior corrosion resistance, making it ideal for harsh environments with chloride presence and induced cracking.
Its advantages include high-temperature strength, cryogenic applications, and resilience in highly corrosive settings. Austenitic stainless steel stands out for its exceptional corrosion resistance and versatility, making it a top choice for critical industrial operations.
Martensitic
Martensitic stainless steel is known for its higher carbon content and enhanced strength through hardening and tempering. It is utilized in various industrial applications requiring moderate corrosion resistance and high mechanical properties.
This stainless steel grade is suitable for chemical industry applications due to its ability to withstand aggressive conditions such as treated fluids and high temperatures. It finds use in pressure vessels, process piping, pharmaceutical equipment, and platform accommodation in the oil and gas sector.
When considering stainless steel maintenance, martensitic steel requires proper care to maintain its corrosion resistance, making regular cleaning essential. The specific grade of martensitic stainless steel chosen should match the properties required for the application while also considering manufacturing processes and cost.
Its unique properties make martensitic stainless steel an innovative choice for challenging chemical industry environments.
Duplex
One of the notable types of stainless steel found in industrial applications is the duplex, known for its microstructure comprising 50% ferritic and 50% austenitic components, providing improved strength and resistance to stress corrosion cracking.
- Duplex Stainless Steel Applications
- Widely used in chemical processing equipment, oil and gas industry, and desalination plants
- Ideal for pressure vessels, process piping, and storage tanks in aggressive environments
- Suitable for applications requiring high strength, resistance to corrosion, and chloride presence
Duplex Stainless Steel Advantages
- Superior Corrosion Resistance
- Exhibits excellent resistance to localized and uniform corrosion
- Withstands aggressive conditions such as high temperatures and corrosive substances
- Ideal for environments with chloride presence and induced cracking
Properties of Duplex Stainless Steel
- High Strength and Toughness
- Offers higher strength than austenitic and ferritic stainless steels
- Maintains good toughness and ductility
- Provides exceptional resistance to pitting and crevice corrosion
Precipitation hardening (PH)
Understanding the process of precipitation hardening (PH) is crucial for comprehending the distinct characteristics and applications of this type of stainless steel in various industrial settings. Precipitation hardening steel is known for its super-strong properties achieved through a unique manufacturing process. Below is a comparison of precipitation hardening steel with other stainless steels.
Properties | Precipitation Hardening Steel |
---|---|
Strength | Exceptionally high |
Corrosion Resistance | Excellent |
Machinability | Good |
Advantages of precipitation hardening steel include its high strength, excellent corrosion resistance, and good machinability. Common applications of precipitation hardening steel are in aerospace components, nuclear reactor vessels, and high-performance equipment. Its unique properties make it suitable for applications requiring high strength and corrosion resistance, setting it apart from other stainless steels.
Duplex stainless steel in the chemical industry
Duplex stainless steel is widely utilized in the chemical industry for its exceptional properties and versatile applications.
It offers high resistance to corrosion, making it suitable for various environments with chloride presence and induced cracking.
Additionally, its ability to withstand aggressive conditions, such as treated fluids and high temperatures, makes it a preferred choice for critical applications in the chemical industry.
applications of duplex stainless steel
Often used in the chemical industry, duplex stainless steel exhibits unique properties that make it suitable for various applications.
-
Duplex stainless steel properties include a microstructure of 50% ferritic and 50% austenitic, providing improved strength and resistance to stress corrosion cracking.
-
Advantages of duplex stainless steel encompass high resistance to corrosion from highly corrosive substances, impressive mechanical characteristics, and the ability to withstand aggressive conditions such as treated fluids and high temperatures.
-
The corrosion resistance of duplex stainless steel makes it suitable for environments with chloride presence and induced cracking, as well as for use in cryogenic applications, elevated temperatures, and highly corrosive environments.
BENEFITS OF DUPLEX STAINLESS STEEL
Benefiting the chemical industry, duplex stainless steel offers a unique combination of properties that make it highly suitable for a wide range of applications. Its exceptional corrosion resistance in aggressive environments, such as those with chloride presence, makes it ideal for chemical processing equipment, storage tanks, and piping systems.
The duplex stainless steel’s microstructure provides enhanced strength and resistance to stress corrosion cracking, making it suitable for use in demanding chemical and petrochemical environments. Its manufacturing process involves carefully controlled composition and heat treatment to achieve the desired properties.
With its impressive mechanical characteristics and ability to withstand treated fluids and high temperatures, duplex stainless steel is a valuable asset in the chemical industry, providing reliability and durability in corrosive environments.
Applications for the chemical and processing industries
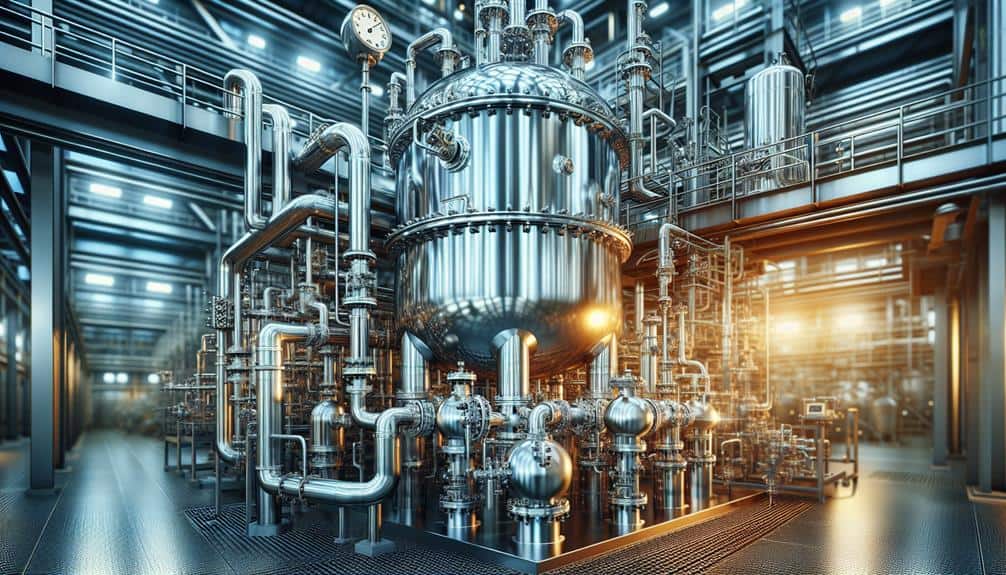
Stainless steel is widely employed in the chemical and processing industries for a multitude of applications, owing to its exceptional strength and resistance to corrosion.
- Stainless steel is extensively used for pressure vessels and process piping in chemical and pharmaceutical industries.
- It’s commonly found in platform accommodation, cable trays, and subsea pipelines in the oil and gas sector.
- Large markets for stainless tanks, pipes, pumps, and valves rely on its durability.
Stainless steel offers numerous benefits in the chemical and petrochemical industries. It provides high resistance to corrosion from highly corrosive substances and impressive mechanical characteristics. Additionally, it can withstand aggressive conditions such as treated fluids and high temperatures, making it suitable for environments with chloride presence and induced cracking.
Moreover, special grades with greater corrosion resistance are used in desalination plants, sewage plants, and offshore oil rigs. Stainless steel’s ability to cope with a variety of raw crudes in petroleum refining further underlines its versatility and utility in these industries.
Applications at Chemical Plants
Stainless steel offers exceptional resistance to everyday corrosion, making it an ideal material choice for a wide range of chemical plant applications. Its ability to withstand the harsh chemicals and oxidizers commonly found in chemical plants ensures longevity and reliability in various components and units.
Moreover, stainless steel’s smooth, non-porous structure makes it easy to clean, contributing to its suitability for use in corrosive environments.
Stainless Steel Resists Everyday Corrosion
The applications of stainless steel in chemical plants demonstrate its exceptional resistance to everyday corrosion, making it an ideal material for various components and units within these industrial settings.
- Stainless steel is a prime choice for fluid systems, ensuring long term durability and reliability in chemical environments.
- It offers the best overall resistance to a wide range of chemicals, providing cost-effective maintenance.
- Stainless steel’s adaptability makes it versatile for process equipment, tanks, and structural elements, contributing to its widespread use in chemical plants.
Stainless steel’s ability to resist corrosion from acids, oxidizers, and harsh chemicals makes it a valuable asset for ensuring longevity and reliability in chemical plants.
Stainless Steel is Easy to Keep Clean
When considering the cleanliness of stainless steel in applications at chemical plants, it’s essential to understand its smooth, non-porous nature and its ease of cleaning.
Stainless steel’s surface durability and chemical resistance make it ideal for maintaining a clean environment in corrosive settings. To ensure stainless steel maintenance, establish a regular cleaning schedule and avoid steam cleaning to prevent contamination.
Resurfacing the metal when needed and avoiding abrasions on the surface are crucial for maintaining its longevity. Proper cleaning not only preserves the stainless steel but also upholds the safety of employees and the environment.
The cost-effectiveness of stainless steel in corrosive environments is evident through its ease of cleaning, longevity, and durability, making it a preferred choice for chemical plant applications.
Frequently Asked Questions
What Are the Specific Properties of Stainless Steel That Make It the Best Choice for Corrosive Environments in the Chemical Industry?
In corrosive environments, stainless steel excels due to its exceptional corrosion resistance, high temperature tolerance, strength, durability, and cost-effectiveness. Its properties make it the optimal choice for the demanding conditions of the chemical industry.
How Do the Properties and Applications of Duplex Stainless Steel Differ From Other Types of Stainless Steel in the Chemical Industry?
In the chemical industry, duplex steel offers superior corrosion resistance, high-temperature strength, and weldability. Its exceptional properties make it a cost-effective choice for demanding applications, ensuring innovation and reliability in harsh environments.
What Are Some Unique and Lesser-Known Applications of Stainless Steel in the Chemical and Processing Industries?
You’ll be amazed by stainless steel’s diverse applications in the chemical and processing industries. From its exceptional surface finishes and heat resistance to its unmatched corrosion resistance, weldability options, and material compatibility, stainless steel excels in these environments.
How Does Stainless Steel Specifically Benefit and Excel in Use Within Chemical Plants, Beyond Its General Applications in the Industry?
When choosing materials, stainless steel excels in chemical plants. Its corrosion resistance, high-temperature capabilities, and cost efficiency make it a superior choice. Additionally, maintenance benefits contribute to its suitability for various applications in chemical plants.
What Are Some Innovative or Unusual Ways That Stainless Steel Is Being Utilized in Chemical Plants, Beyond the Commonly Known Applications?
You’re surprised to learn that stainless steel is creatively used in chemical plants for innovative purposes beyond the norm. Uncommon applications include its use in structural shapes, tanks, and process equipment, showcasing its adaptability and inventive solutions.
Conclusion
In conclusion, stainless steel’s exceptional resistance to corrosion and its ability to withstand harsh environments make it the ideal choice for the chemical industry.
Its wide range of applications in chemical plants and processing industries, along with its different types and unique characteristics, highlight its significance in ensuring the safety and reliability of equipment.
Its use in corrosive environments, such as in the oil & gas industry, further solidifies its importance in maintaining operational efficiency and long-term durability.