High carbon steel tubing is known for its exceptional strength, durability, and corrosion resistance, essential in demanding industrial applications. Manufactured through processes like hot rolling and cold drawing, its compositional properties enhance strength and wear resistance while sometimes reducing weldability. Carbon content selection and heat treatment are critical for desired properties like high strength and hardness. Ensuring top-notch strength and durability, high carbon steel tubes find use in automotive, construction, industrial machinery, agricultural equipment, and aerospace applications. These tubes offer high tensile strength, hardness, and wear resistance but require attention to welding and machining due to their high carbon content.
Key Takeaways
- High carbon steel tubes offer exceptional strength and durability.
- They are resistant to corrosion, heat, and impact, ideal for demanding applications.
- Machinability and weldability are key features for fabrication versatility.
- Compositional properties contribute to high strength, hardness, and wear resistance.
- Understanding properties and applications is crucial for effective use in various industries.
Importance and Wide Application of High Carbon Steel Tube
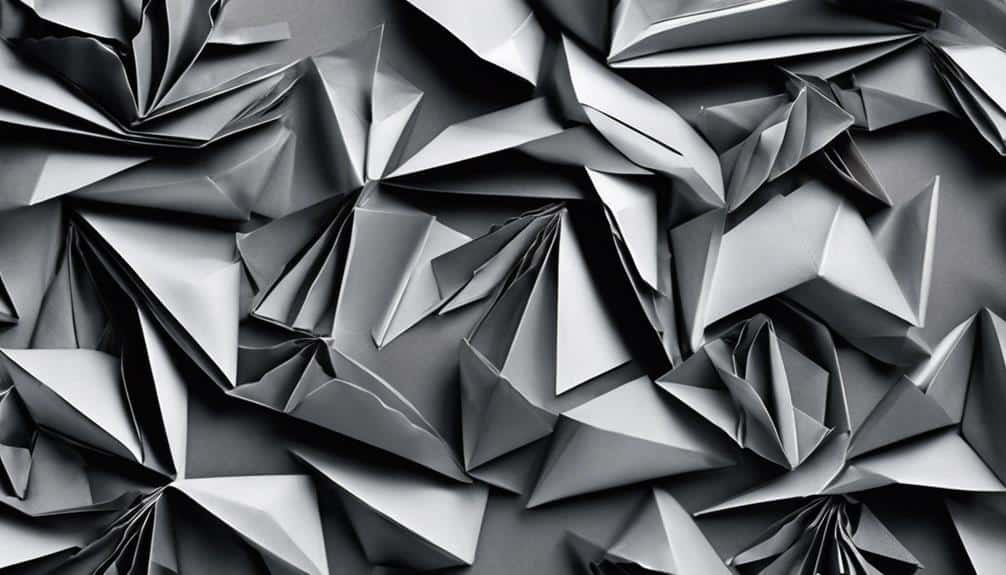
High Carbon Steel tubing plays an essential role in various industries due to its exceptional strength and durability properties. With high strength and toughness, these tubes offer excellent resistance to corrosion, making them ideal for harsh environments. Their heat resistance and impact resistance further enhance their durability, ensuring longevity in demanding applications.
High Carbon Steel tubes are known for their machinability and weldability, allowing for easy fabrication and customization. The versatility of these tubes enables their use in diverse applications, from structural frameworks to machinery components. Additionally, their cost-effectiveness makes them a preferred choice for many industries seeking reliable and long-lasting materials.
How are high carbon steel tubes manufactured?
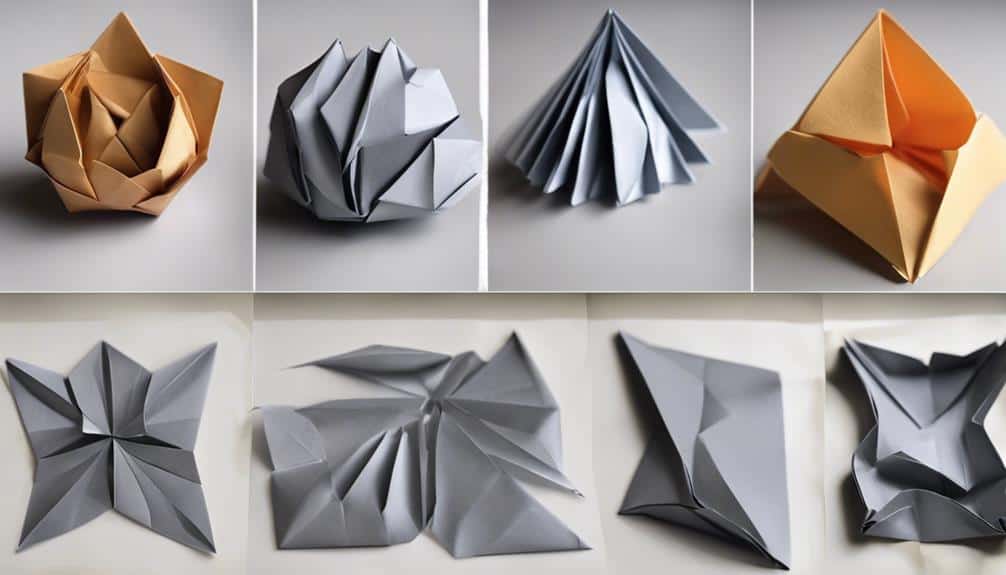
High carbon steel tubes are typically manufactured through processes like hot rolling, cold drawing, or a combination of both.
The compositional properties of high carbon steel tubes, such as their high carbon content, contribute to their exceptional strength and hardness.
Understanding both the advantages, like superior wear resistance, and the disadvantages, such as decreased weldability, is important when considering the use of high carbon steel tubes in various applications.
The process of making high carbon steel tubes
The manufacturing process of high carbon steel tubes involves a series of precise steps to guarantee the quality and durability of the final product. Initially, the carbon content is carefully selected to ensure the desired strength and hardness.
Tube forming is then carried out through processes like hot or cold rolling to shape the steel into tubes. Alloy additions may be made to improve specific properties such as corrosion resistance or strength.
Heat treatment is essential to refine the microstructure and achieve the desired mechanical properties. Finally, surface finishing techniques like polishing or coating are applied to improve the aesthetics and protect against corrosion, ensuring a high-quality end product.
Compositional properties of high carbon steel tubes
Manufacturing high carbon steel tubes involves meticulous control over the carbon content to guarantee specific strength and hardness requirements are met during the tube forming process. The chemical composition of high carbon steel tubes typically includes carbon content ranging from 0.55% to 0.95%, with additional elements like manganese, silicon, and sometimes small amounts of other alloying elements to enhance mechanical properties.
Heat treatment plays a pivotal role in achieving the desired strength and hardness levels. High carbon steel tubes exhibit excellent mechanical properties, making them suitable for applications requiring high strength and wear resistance. However, they may have lower corrosion resistance compared to other steel types. Their welding capabilities can vary depending on the specific composition and heat treatment used.
Advantages and disadvantages of high carbon steel tube
Utilizing precise control over carbon content and strategic heat treatment processes, the manufacturing of high carbon steel tubes aims to optimize strength and hardness properties to meet specific application requirements.
High carbon steel tubes offer several advantages such as exceptional durability, high strength, and good wear resistance, making them suitable for heavy-duty applications. However, these tubes tend to have lower weldability due to their high carbon content, requiring special welding techniques.
Additionally, high carbon steel tubes are more susceptible to corrosion compared to low carbon steel counterparts, necessitating proper maintenance and protective coatings to enhance their corrosion resistance. Despite these drawbacks, the superior mechanical properties of high carbon steel tubes make them valuable in applications where strength and hardness are paramount.
Application areas for high carbon steel tubes

Significant industries rely on high carbon steel tubing for their structural integrity and durability in demanding environments.
High carbon steel tubes find applications in various sectors such as automotive components, where they are used for manufacturing exhaust systems, drive shafts, and suspension components.
In construction materials, these tubes are essential for scaffolding, bridges, and high-rise buildings due to their strength and resistance to corrosion.
Industrial machinery benefits from high carbon steel tubes in hydraulic systems, conveyor belts, and heavy-duty equipment.
Agricultural equipment, including plows, cultivators, and irrigation systems, also utilize these tubes for their robust nature.
Moreover, high carbon steel tubing is critical in aerospace applications for manufacturing aircraft components that require high strength and reliability in extreme conditions.
Characteristics of high carbon steel tubes
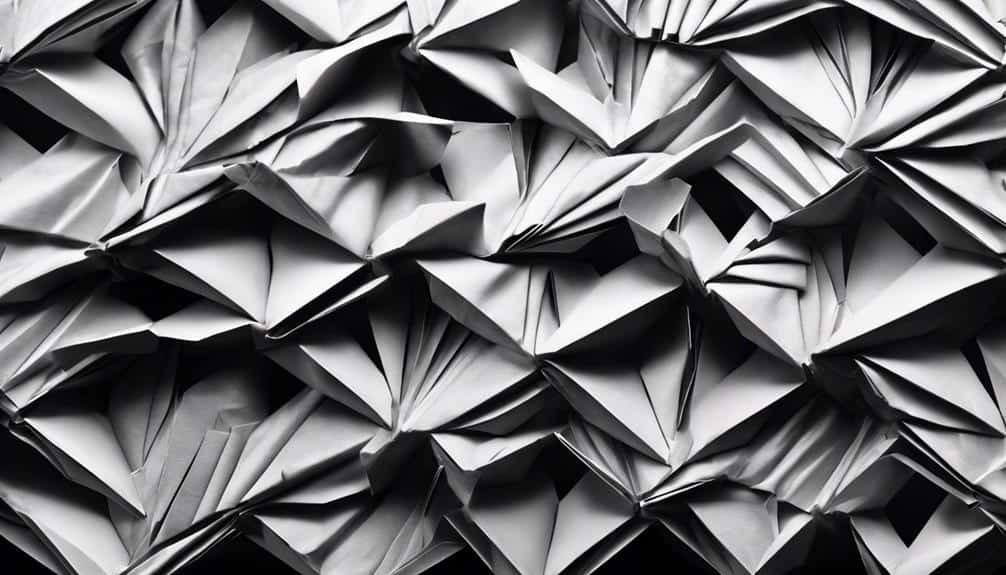
High carbon steel tubing exhibits exceptional strength and durability due to its unique composition and heat treatment processes. The table below outlines key characteristics of high carbon steel tubes, highlighting aspects such as corrosion resistance, weldability, impact resistance, cost-effectiveness, and more.
Characteristic | Description |
---|---|
Strength | High tensile strength and hardness make it suitable for demanding applications. |
Durability | Resistant to wear and tear, ensuring longevity and reliability. |
Weldability | Requires preheating before welding due to high carbon content. |
Machinability | Machining may be challenging but achievable with proper tools and techniques. |
Flexibility | Offers moderate flexibility, depending on the specific alloy composition. |
Frequently Asked Questions
What Are the Common Challenges Faced During the Welding Process of High Carbon Steel Tubes?
Challenges during the welding process of high carbon steel tubes include managing the heat treatment to prevent brittleness, guaranteeing effective corrosion prevention measures, and addressing the environmental impact due to high carbon content.
Cost comparison with other materials, exploring recycling potential, and considering repurposing options are also significant factors.
Welding high carbon steel tubes requires precision and expertise to overcome these challenges and ensure the structural integrity and longevity of the final product.
Are There Any Specific Maintenance Requirements for High Carbon Steel Tubes to Prevent Corrosion?
To maintain high carbon steel tubes and prevent corrosion, specific maintenance requirements are essential. Implementing preventive measures such as regular inspections, applying protective coatings, and utilizing appropriate surface treatments can enhance corrosion resistance.
Inspection techniques like visual inspections and non-destructive testing further aid in identifying early signs of corrosion. Employing these maintenance practices guarantees the longevity and best performance of high carbon steel tubing in various applications.
How Does the Cost of High Carbon Steel Tubes Compare to Other Types of Steel Tubing?
When comparing the cost of high carbon steel tubes with other steel tubing types, factors such as material procurement, manufacturing processes, and specific alloy compositions must be considered. High carbon steel tubes generally have a higher cost due to the quality of the raw materials and the complex manufacturing techniques involved.
The welding challenges, corrosion prevention methods, environmental impact, and recycling possibilities of high carbon steel tubes also affect their overall cost competitiveness in the market.
Are There Any Environmental Considerations to Take Into Account When Using High Carbon Steel Tubes?
When assessing the use of high carbon steel tubes, it is essential to contemplate the environmental impact. Sustainable practices, such as recycling options and minimizing the carbon footprint, play a crucial role in mitigating the ecological consequences of utilizing high carbon steel.
Exploring eco-friendly alternatives can further enhance environmental stewardship in industries where high carbon steel tubing is prevalent. Adopting such measures is imperative for fostering a greener and more sustainable future.
Can High Carbon Steel Tubes Be Easily Recycled or Repurposed at the End of Their Life Cycle?
High carbon steel tubes can be recycled or repurposed at the end of their life cycle, offering sustainable disposal options. Recycling facilities can process these tubes for reuse, contributing to resource conservation.
Repurposing opportunities include upcycling possibilities, promoting a circular economy and minimizing environmental impact. Material sustainability is enhanced through eco-friendly alternatives, aligning with waste management practices and promoting a more sustainable future.
Conclusion
To sum up, high carbon steel tubes play a crucial role in various industries due to their strength, durability, and resistance to wear and tear. They are manufactured through a precise process involving carbon content manipulation and heat treatment.
The application areas for high carbon steel tubes are vast, ranging from automotive to construction. Essentially, high carbon steel tubes are the backbone of many industrial operations, making them an essential component in the modern world.
To put it simply, they are the ‘driving force‘ behind many successful projects.