You might be thinking that stainless steel is just another material in the mining industry, but its impact goes far beyond that assumption. The versatility and durability of stainless steel make it an integral component of mining operations, from equipment to infrastructure.
But what exactly sets stainless steel apart and how does it contribute to the efficiency and sustainability of mining practices? Let’s explore the crucial role that stainless steel plays in the mining industry and how it addresses the unique challenges faced in this sector.
Key Takeaways
- Stainless steel and duplex stainless steel are widely used in the mining industry due to their low cost, high strength, lightweight, ability to resist corrosion, durability, and sustainability.
- Stainless steel is easy to clean and reduces the risk of contamination, making it ideal for storing substances in the mining industry.
- Stainless steel is versatile and used in various applications in mining, including tools, drill rigs, demolition equipment, grinding media, mining screens, fluidized bed boilers, pumps, heat exchangers, vessels, pipes, tanks, cathode plates, mass excavators, bulldozers, shovels, crushers, and workbenches.
- Duplex steel is in high demand in the mining industry due to its higher strength than carbon steel and extremely high level of corrosion resistance.
Stainless steel and the mining industry
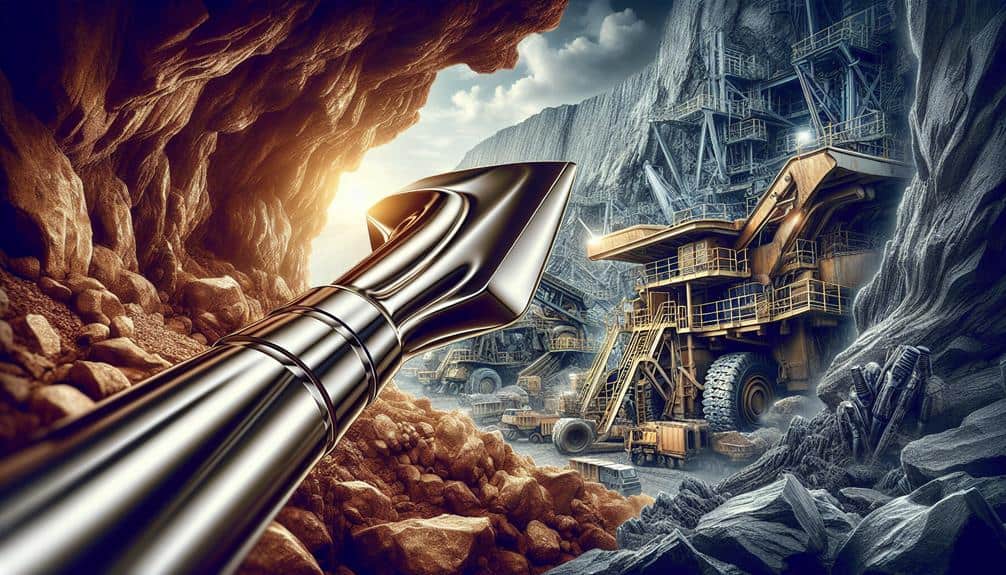
Stainless steel is extensively utilized in the mining industry due to its exceptional properties, including low cost, high strength, corrosion resistance, and sustainability, making it an indispensable material for various applications in mining equipment and machinery. Its cost-effectiveness and durability have led to numerous innovations in mining technology. The sustainability benefits of stainless steel in mining operations are evident, as it reduces environmental impact and contributes to the industry’s efforts to minimize emissions.
The corrosion resistance of stainless steel is a critical factor in its applications for mining equipment. This resistance ensures the longevity of mining machinery even in harsh environments, contributing to the overall efficiency and reliability of mining operations. Additionally, the future prospects for stainless steel in mining technology are promising, with an increasing demand for its use in structural components, tools, drill rigs, pumps, heat exchangers, and various other equipment at mining sites.
WEAR RESISTANT STEELS FOR THE MINING INDUSTRY
When it comes to the mining industry, wear resistant steels play a crucial role in maintaining equipment longevity and performance.
Abrasion-resistant steel plates, in particular, are designed to withstand the harsh conditions of mining operations, providing high resistance to abrasion, wear, tear, and impact.
These steels are widely used in mining applications such as liners, buckets, chutes, conveyors, and other structural elements, ensuring durability and operational efficiency in critical areas of the mining process.
abrasion-resistant steel plate
Abrasion-resistant steel plates are crucial components in the mining industry, offering unparalleled durability and protection against wear and tear in critical applications such as liners and structural elements for various mining equipment.
These wear-resistant steel plates play a vital role in enhancing the longevity and reliability of mining machinery and infrastructure.
The benefits of stainless steel in mining are further amplified by its exceptional corrosion resistance, ensuring minimal material depreciation even in the harshest mining environments.
Additionally, the impact of stainless steel on mining sustainability is significant, with its capability for efficient recycling contributing to the industry’s environmental initiatives.
Applications of Stainless Steel in the Mining Industry
Steel is widely utilized in a multitude of applications within the mining industry due to its exceptional properties and benefits. Stainless steel, in particular, offers significant corrosion resistance benefits, environmental sustainability, and cost advantages. Its diverse applications in mining equipment materials make it an indispensable choice. Here’s a brief overview:
Applications | Benefits |
---|---|
Tools | Corrosion resistance, durability, sustainability |
Drill rigs | Low cost, high strength |
Demolition equipment | Lightweight, corrosion resistance, sustainability |
Stainless steel is extensively employed in various mining equipment and machinery. Its use in mass excavators, bulldozers, shovels, and crushers showcases its robustness and durability. Additionally, stainless steel’s cost advantages compared with other materials make it an economically viable choice for the mining industry. The environmental sustainability and corrosion resistance benefits of stainless steel further solidify its position as a preferred material for a wide array of applications in the mining sector.
How stainless steel helps to reduce environmental impact of mining
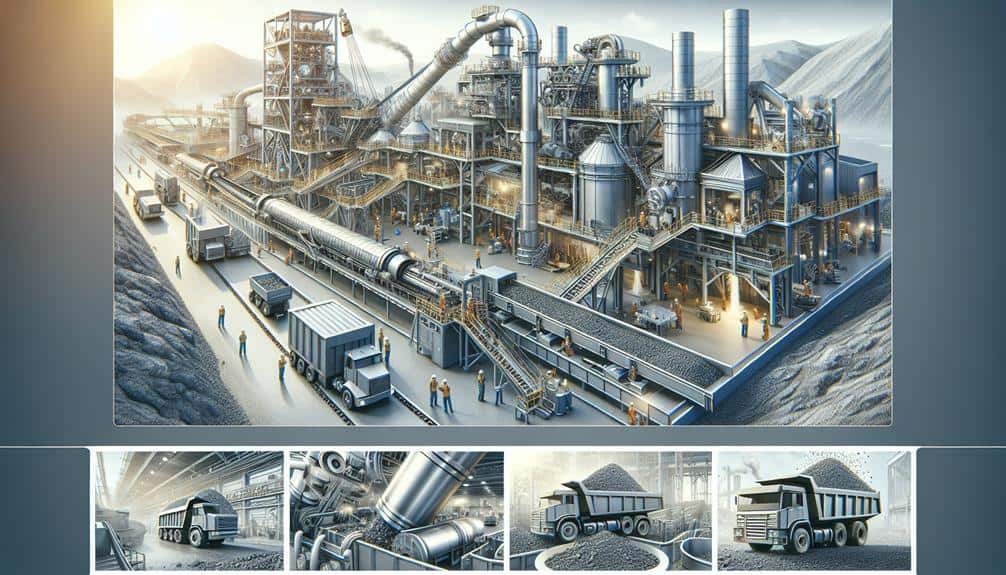
The extensive use of stainless steel in various mining equipment and machinery not only showcases its robustness and durability but also highlights its crucial role in reducing the environmental impact of mining operations. Stainless steel contributes to sustainable mining practices through its corrosion resistance in mining equipment, promoting longevity and durability in mining operations. This aids in reducing the environmental impact in multiple ways:
-
Renewable energy integration
-
Stainless steel facilitates the development of sustainable mining practices by supporting the integration of renewable energy sources into mining operations, thereby reducing the reliance on traditional energy sources.
-
Recycling and circular economy
-
Stainless steel’s recyclability and long-life properties promote the implementation of circular economy principles within the mining industry, minimizing waste and promoting resource efficiency.
-
Efficient ore-processing practices
-
Stainless steel’s strength and corrosion resistance enable efficient ore-processing practices, reducing the volume of material that requires potentially hazardous refining methods and minimizing the environmental impact.
Types of stainless use used in the mining industry
Stainless steel plays a crucial role in the mining industry. Its applications range from hot rolled coils and sheets to wear resistant steel. These types of stainless steel are commonly used in mining equipment and machinery. This is due to their high strength and wear resistance properties.
In addition, hot rolled plates are also essential for structural elements within mining operations. They are used in buckets, skips, chutes, bins, ore pockets, conveyors, and dump trucks. These structural elements require the strength and durability provided by stainless steel.
hot rolled coils
Hot rolled coils, commonly used in the mining industry, are thin flat pieces of steel wound up into coils that offer weight-saving and aesthetic value while providing high formability and tensile strength.
-
Corrosion resistance in mining:
Hot rolled coils with corrosion resistance properties are vital for mining equipment and structures, enhancing longevity in harsh environments. -
Impact of hot rolling on steel properties:
Hot rolling enhances steel strength and ductility, crucial for withstanding the demanding conditions in the mining industry. -
Hot rolling process efficiency:
The hot rolling process ensures efficient production of coils, meeting the high demand for steel in mining applications.
Hot rolled coil technology innovations continually improve steel properties, expanding its applications across industries, including automotive, construction, energy, and manufacturing.
hot rolled sheets
After discussing the significance of hot rolled coils in the mining industry, it’s pertinent to explore the application of hot rolled sheets and their specific types of stainless steel used in this sector.
Hot rolled steel production involves the initial process of shaping steel at high temperatures, resulting in sheets with desirable properties. The advantages of hot rolled sheets include improved malleability, making them suitable for various mining applications such as structural components, equipment, and machinery.
These sheets exhibit excellent strength, durability, and are resistant to corrosion, making them ideal for harsh mining environments. Additionally, hot rolled sheet suppliers like Metal Special offer a wide range of high-quality steel sheets, meeting international standards and catering to diverse needs across different industries, including mining, automotive, energy, and construction.
hot rolled plates
When considering the types of stainless steel used in the mining industry, it’s imperative to analyze the specific applications and performance characteristics of hot rolled plates.
-
Corrosion resistance in mining
-
Hot rolled plates offer exceptional resistance to corrosion, crucial for mining operations exposed to harsh environments.
-
High temperature applications
-
These plates are designed to withstand high temperatures, making them suitable for various heat-intensive mining processes.
-
Sustainability in mining operations
-
Utilizing hot rolled plates promotes sustainability due to their recyclability and long lifespan, aligning with eco-friendly mining practices.
Hot rolled plates also offer cost-effectiveness, as they can be customized to meet specific mining requirements, providing a durable and reliable solution for various structural and equipment needs in the mining industry.
wear resistant steel
Wear-resistant steel, also known as abrasion-resistant steel, plays a critical role in the mining industry due to its high-carbon alloy composition that provides increased hardness and toughness essential for withstanding the harsh conditions of mining operations.
The properties of wear-resistant steel, including its high tensile strength and wear resistance, make it suitable for various mining applications such as liners, buckets, chutes, and conveyors.
Different grades of wear-resistant steel, such as Raex 500 plates, AR400, AR450, and Hardox steel, offer favorable hardness, impact toughness, and durability, extending the lifespan of machinery and structural components.
The manufacturing process involves hardening the steel by adding alloying elements like manganese, chromium, nickel, vanadium, and boron.
This results in a material that can last up to four times longer than conventional high-strength steel, providing significant benefits to the mining industry.
Frequently Asked Questions
How Does the Use of Stainless Steel in the Mining Industry Compare to Other Materials in Terms of Cost and Durability?
In comparison to other materials, stainless steel in the mining industry offers cost effectiveness, superior corrosion resistance, and longevity benefits. Its material selection is pivotal for durability, making it a top choice for various mining applications.
Are There Specific Types of Stainless Steel That Are More Commonly Used in the Mining Industry, and What Are Their Unique Properties?
Specific types of stainless steel commonly used in the mining industry include duplex stainless steel. Their unique properties include high strength, corrosion resistance, and durability. These properties make them cost-effective, efficient, and environmentally beneficial for mining applications.
What Are the Specific Environmental Benefits of Using Stainless Steel in the Mining Industry, and How Does It Contribute to Reducing Emissions?
Using stainless steel in the mining industry reduces emissions by promoting environmental sustainability. Its durability and unique properties contribute to efficiency and safety, while its recyclability and reuse opportunities offer cost-effective solutions.
Can Stainless Steel Be Recycled and Reused in the Mining Industry, and What Are the Challenges and Opportunities Associated With This Process?
Yes, stainless steel can be recycled and reused in the mining industry, presenting opportunities for reducing environmental impact. Challenges include material comparison, durability assessment, and addressing recycling challenges to maximize the potential for reuse.
How Does the Use of Wear Resistant Steel in the Mining Industry Impact the Overall Efficiency and Safety of Mining Operations?
Wear resistant steel impacts mining operations by improving efficiency and safety, providing cost advantages, and ensuring material durability. Despite recycling challenges, its environmental benefits make it a crucial innovation in the industry.
Conclusion
You’ve now uncovered the vital role that stainless steel plays in the mining industry. Like a sturdy shield, it withstands the harsh conditions of mining operations, offering strength and corrosion resistance.
Its use in critical equipment helps to reduce emissions and limit environmental footprint, contributing to a more sustainable and efficient mining industry.
With its versatile applications and recyclability, stainless steel is an indispensable ally in the quest for responsible mining practices.