Steel pipes encompass a variety of types like seamless, welded, carbon, alloy, stainless, galvanized, and structural steel tubing. Each type offers specific properties and benefits for diverse applications. Understanding the manufacturing processes and characteristics of these steel pipes guarantees structural integrity and durability. Alloy steel tubing provides exceptional strength, while stainless steel tubing offers corrosion resistance and versatility. Galvanized steel tubing with zinc coating is ideal for outdoor use, and structural steel tubing supports heavy loads in construction. Explore further to discover how each type suits different industries and applications.
Overview of Steel Tubing Types
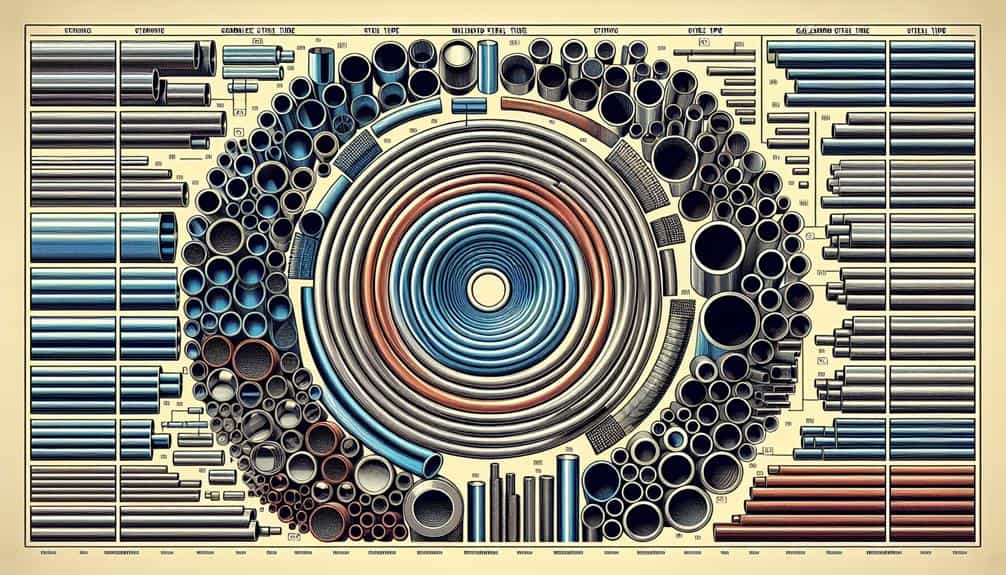
Steel tubing encompasses a diverse range of types, each tailored for specific industrial applications and structural requirements. From seamless tubes to welded tubes, the variations in manufacturing processes yield distinct properties that determine the tubing’s performance under different conditions.
The choice of steel tubing type is pivotal in ensuring structural integrity, corrosion resistance, and durability in various applications such as construction, automotive, and oil and gas industries.
The selection of steel tubing is influenced by factors like the required strength, ductility, and resistance to external elements. Seamless tubing, produced through extrusion or rotary piercing, offers uniformity and high pressure-bearing capabilities, ideal for critical applications like hydraulic systems. On the other hand, welded tubing, created through fusion welding of steel strips, provides cost-effective solutions for less demanding structural needs.
Understanding the characteristics and capabilities of different steel tubing types is essential for engineers, architects, and manufacturers to make informed decisions that align with the specific requirements of their projects.
Types of steel tubing
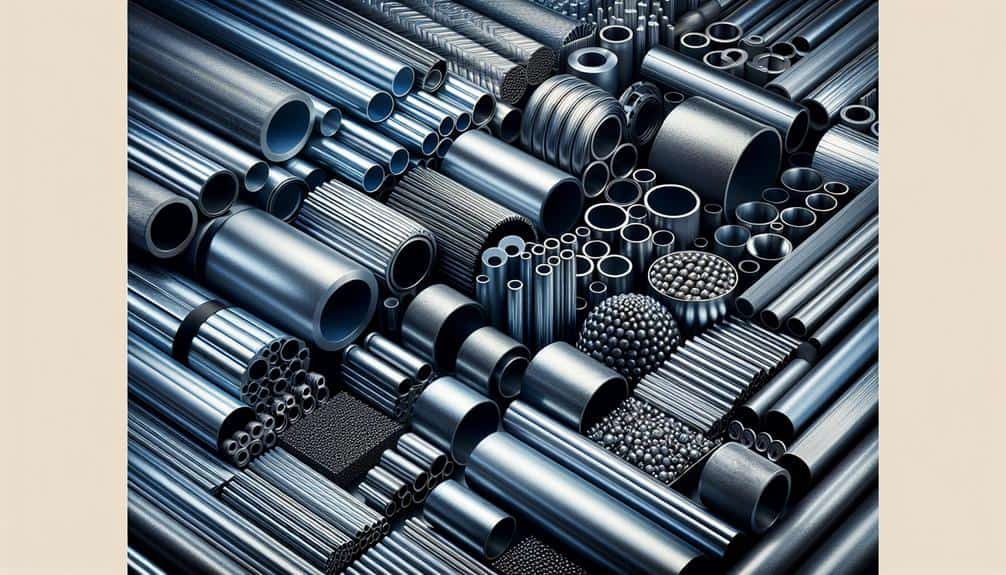
The various types of steel tubing encompass a range of materials and applications.
Carbon steel tubing is known for its strength and cost-effectiveness, while alloy steel tubing offers enhanced mechanical properties due to its composition.
Stainless steel tubing is corrosion-resistant and ideal for applications requiring hygiene and durability, and galvanized steel tubing is coated with zinc for added protection against corrosion.
Structural steel tubing provides robust support in construction and infrastructure projects.
Carbon steel tubing
Among the various types of steel tubing available in the market, carbon steel tubing stands out for its versatility and durability in industrial applications. Carbon steel tubing is known for its high strength, impact resistance, and ability to withstand harsh environmental conditions.
It is commonly used in structural, mechanical, and hydraulic applications where reliability is paramount. The manufacturing process of carbon steel tubing involves forming and welding steel strips or plates, followed by further shaping and sizing to meet specific requirements.
This type of tubing is cost-effective, readily available, and can be easily customized to suit different project needs. Carbon steel tubing is favored in industries such as construction, automotive, and infrastructure for its excellent performance and longevity.
Alloy steel tubing
With their enhanced properties and specific alloy compositions, alloy steel tubing offers a wide range of applications and benefits in various industrial sectors. Alloy steel tubing is known for its exceptional strength, toughness, and corrosion resistance, making it ideal for demanding applications.
The alloying elements, such as chromium, molybdenum, and nickel, impart unique characteristics to the steel, allowing for increased durability and performance under high temperatures and pressures. Additionally, alloy steel tubing can be tailored to meet specific requirements by adjusting the alloy composition, heat treatment, and manufacturing processes.
Common types of alloy steel tubing include chrome-moly (chromium-molybdenum) and nickel-chrome-moly, each suited for different applications based on their alloy content and properties.
Stainless steel tubing
Stainless steel tubing encompasses a variety of steel tubing types distinguished by their specific alloy compositions and properties. Commonly used grades include 304 and 316 stainless steel, known for their corrosion resistance, high-temperature strength, and durability.
Applications for stainless steel tubing span various industries, such as automotive, aerospace, medical, and construction, where its superior properties are highly valued. The seamless construction of stainless steel tubing guarantees a smooth interior surface, making it suitable for applications requiring high purity, such as in the food and beverage industry.
Additionally, stainless steel tubing can be easily fabricated, welded, and formed into different shapes to meet specific project requirements, offering versatility and reliability in demanding environments.
Galvanized steel tubing
What distinguishes galvanized steel tubing from other types of steel tubing is its protective zinc coating, which provides enhanced corrosion resistance and longevity in various applications.
Galvanized steel tubing is manufactured by immersing the steel tube in a bath of molten zinc, which forms a metallurgical bond with the steel. This process, known as hot-dip galvanization, creates a barrier that shields the underlying steel from environmental factors that could lead to rust and corrosion.
Galvanized steel tubing is commonly used in outdoor construction projects, fencing, handrails, and plumbing systems where exposure to moisture and harsh elements is a concern. Its durability and cost-effectiveness make it a popular choice for applications requiring robust protection against corrosion.
Structural steel tubing
Structural steel tubing encompasses a diverse range of steel tubes specially designed and manufactured to support various structural applications in construction and engineering projects. These tubes are typically produced with high strength to withstand heavy loads and harsh environmental conditions. Common shapes include round, square, and rectangular tubes, each offering specific advantages based on the structural requirements.
Round tubes are often preferred for their uniform strength distribution, while square and rectangular tubes excel in applications needing flat surfaces for joining or aesthetics. Structural steel tubing is commonly used in building frames, bridges, and infrastructure due to its durability and versatility. Understanding the different types and sizes of structural steel tubing is essential for ensuring the stability and longevity of construction projects.
Uses of different types of steel tubes
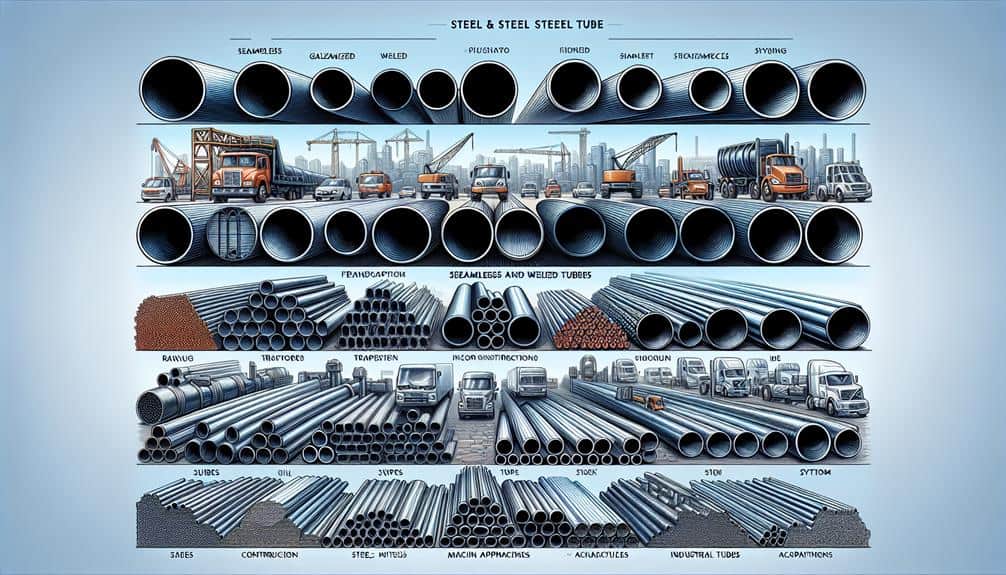
The utilization of various types of steel tubes in industries is diverse and vital.
Carbon steel tubing finds applications in structural components and machinery.
Alloy steel tubing is favored for its strength and heat resistance in high-temperature environments, while stainless steel tubing is widely used in food processing, chemical, and medical industries for its corrosion resistance properties.
Galvanized steel tubing is employed in outdoor structures due to its rust-prevention characteristics, and structural steel tubing is commonly seen in construction for its load-bearing capabilities.
Uses of Carbon steel tubing
Carbon steel tubing is widely utilized in various industries for its strength, durability, and versatility in applications requiring robust structural components. This type of tubing finds extensive use in sectors such as construction, automotive, manufacturing, and infrastructure. Below is a table showcasing some common uses of carbon steel tubing:
Industry | Application | Specific Use |
---|---|---|
Construction | Support structures | Beams, columns, trusses |
Automotive | Exhaust systems | Exhaust pipes, mufflers |
Manufacturing | Machinery | Conveyor systems, hydraulic cylinders |
Infrastructure | Water transportation | Water pipelines, drainage systems |
Uses of Alloy steel tubing
Alloy steel tubing is widely employed in diverse industries for its exceptional mechanical properties and corrosion resistance, serving critical roles in applications requiring specialized materials.
Some common uses of alloy steel tubing include:
-
Oil and Gas Industry: Alloy steel tubing is utilized in oil rigs, pipelines, and refineries due to its high strength and resistance to harsh operating conditions.
-
Automotive Sector: Alloy steel tubing is integral in manufacturing components such as axles, drive shafts, and suspension systems for its durability and toughness.
-
Aerospace Applications: Alloy steel tubing is pivotal in aircraft construction for its lightweight yet strong properties, ensuring structural integrity.
-
Industrial Machinery: Alloy steel tubing is used in the fabrication of heavy machinery and equipment where high strength and wear resistance are essential.
Uses ofStainless steel tubing
Stainless steel tubing finds widespread application across various industries due to its superior corrosion resistance and sanitary properties, serving pivotal roles in specialized environments requiring high-quality materials.
In the medical field, stainless steel tubing is used for surgical instruments, medical implants, and hospital equipment due to its biocompatibility and resistance to sterilization methods.
In the food and beverage industry, it is employed for processing equipment, storage tanks, and piping systems, ensuring product purity and preventing contamination.
Additionally, stainless steel tubing is utilized in construction for structural support, handrails, and architectural features due to its durability and aesthetic appeal. Its versatility, strength, and resistance to extreme temperatures make it indispensable in demanding industrial settings.
Uses ofGalvanized steel tubing
Galvanized steel tubing is widely utilized in various industries for its exceptional corrosion resistance and longevity, making it a preferred choice for applications requiring durability and reliability.
-
Construction: Used in structures like handrails and fencing due to its strength and rust resistance.
-
Water Transmission: Ideal for plumbing and water distribution systems because of its resistance to corrosion.
-
Outdoor Applications: Commonly used in outdoor signage and playground equipment for its weather-resistant properties.
-
HVAC Systems: Employed in heating, ventilation, and air conditioning systems for its durability and ability to withstand harsh environmental conditions.
Uses ofStructural steel tubing
Structural steel tubing is extensively utilized across diverse industries for its superior strength and versatility in various applications requiring robust structural support and stability. In construction, it is commonly used for framing, trusses, and columns due to its high load-bearing capacity.
In the automotive industry, structural steel tubing is essential for manufacturing roll cages and chassis components to enhance vehicle safety. Additionally, in the manufacturing sector, it serves as support structures for conveyor systems and equipment.
The aerospace industry also benefits from structural steel tubing for constructing aircraft frames and support structures. With its exceptional durability and resistance to corrosion, structural steel tubing is indispensable for applications demanding reliable and long-lasting structural integrity.
What are the shapes of steel tubes?
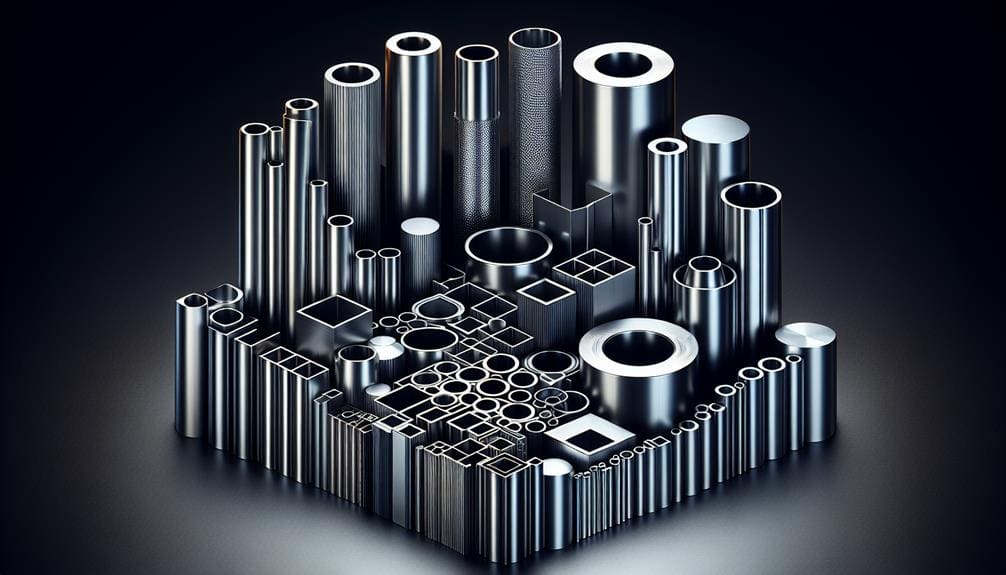
The shapes of steel tubes vary to accommodate different structural requirements and functions. Common shapes include:
- Round tubes
- Square tubes
- Rectangular tubes
Each shape offers distinct properties suitable for various applications. Understanding the characteristics and intended uses of these shapes is essential in selecting the most appropriate steel tube for a specific project.
Characteristics and uses of different shapes of steel tubes
Featuring a variety of shapes such as round, square, and rectangular, steel tubes are utilized across numerous industries for their diverse structural applications. These different shapes offer unique characteristics and benefits depending on the specific requirements of the project.
Here are some common shapes of steel tubes and their typical uses:
-
Round Tubes – Ideal for applications requiring high pressure or fluid transfer.
-
Square Tubes – Often used in construction for frames and support structures due to their flat sides.
-
Rectangular Tubes – Suitable for lightweight construction or architectural purposes.
-
Oval Tubes – Used in furniture making or automotive applications due to their aesthetic appeal and strength.
What are the processes for manufacturing steel pipes?
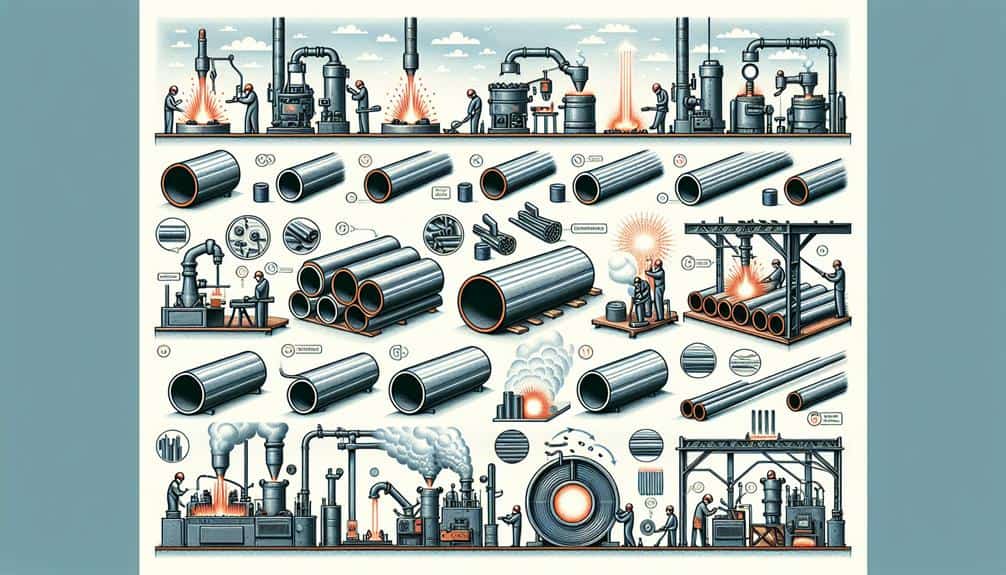
Various manufacturing processes are utilized in the production of steel pipes, each with its own unique characteristics and advantages. Understanding the differences between these processes is vital in determining the quality, strength, and durability of the final product.
What is the difference between the different manufacturing processes?
Different methods employed in the manufacturing of steel pipes involve intricate processes that play a pivotal role in determining the properties and quality of the final product. These processes include:
-
Seamless Process: Involves the creation of pipes without a welded seam, resulting in a smoother surface finish and greater strength.
-
Electric Resistance Welding (ERW): Utilizes electrical current to melt the edges of the steel and create a joint, suitable for high-speed production of pipes.
-
Submerged Arc Welding (SAW): Involves the formation of a weld by heating the workpiece with an arc between a bare metal electrode and the workpiece.
-
Double Submerged Arc Welding (DSAW): Similar to SAW but involves welding both inside and outside of the pipe, resulting in a strong, leak-resistant seam.
How do I choose a steel pipe size?
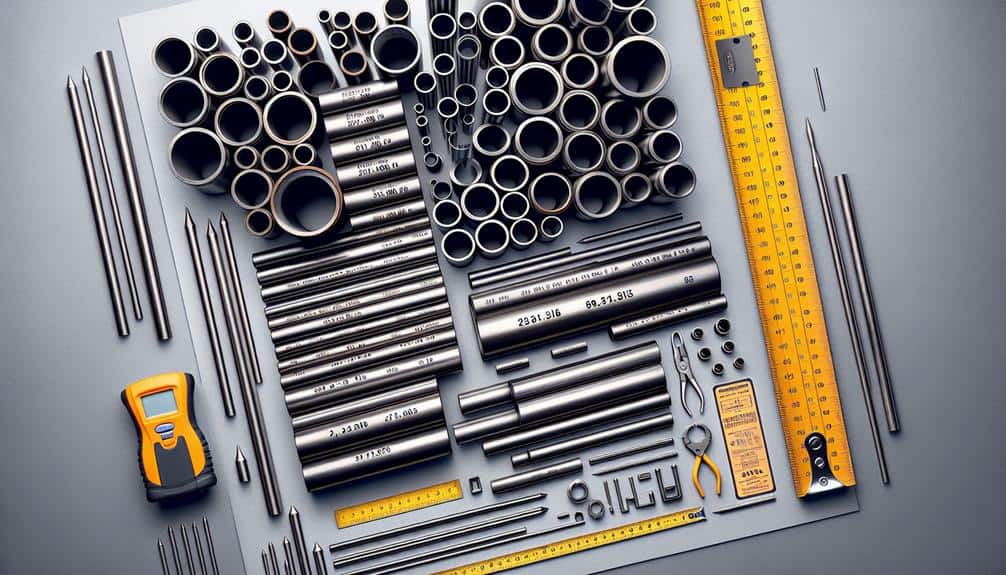
Selecting the appropriate steel pipe size involves careful consideration of factors such as flow rate, pressure requirements, and structural support needs.
The flow rate of the material traveling through the pipe is a critical factor in determining the pipe size. Higher flow rates typically require larger diameter pipes to guarantee efficient transport without excessive pressure drops.
Pressure requirements, including both internal pressure from the material being transported and external environmental factors, also play a significant role in size selection. Pipes must be able to withstand the pressures they will be subjected to without leaking or failing.
Additionally, the structural support needs of the pipe must be evaluated to ensure that it can bear the weight of the material inside as well as any external loads.
Properly sizing a steel pipe is essential to ensure top performance and longevity in various applications.
How to buy the right steel pipe for us?
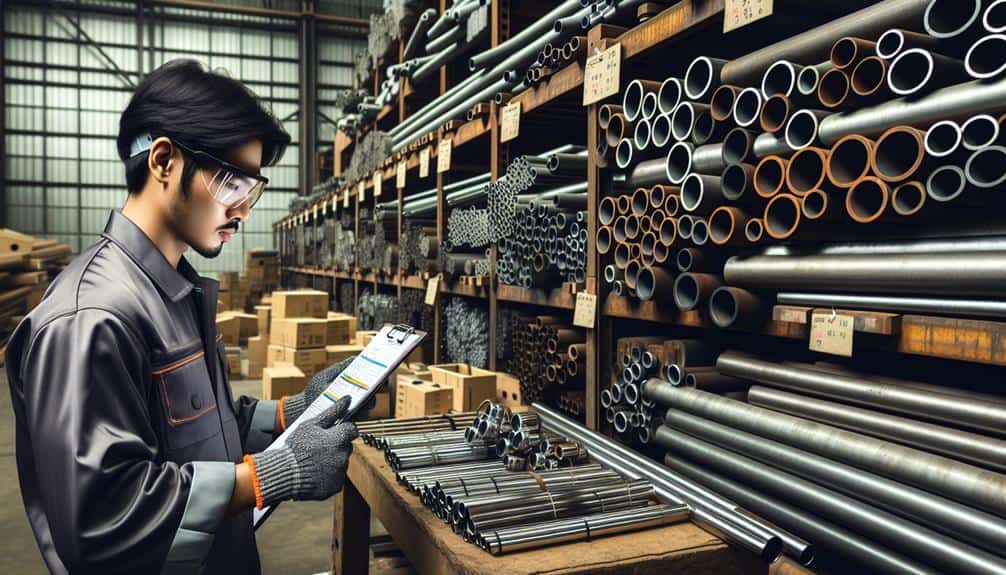
When purchasing a steel pipe, it is crucial to consider aspects such as material composition, size specifications, and intended application to guarantee optimal performance and durability. Here are four key steps to assist you in selecting the right steel pipe:
-
Establish Material Composition: Choose between carbon steel, alloy steel, or stainless steel based on factors like corrosion resistance, strength requirements, and cost-effectiveness.
-
Take into Account Size Specifications: Consider the outer diameter, wall thickness, and length of the pipe to ensure compatibility with your project requirements.
-
Assess End Connections: Determine the type of end connections required, such as threaded, welded, or flanged ends, depending on how the pipe will be installed and connected to other components.
-
Examine Standards and Certifications: Confirm that the steel pipe complies with industry standards like ASTM, ASME, or API, and verify certifications like ISO 9001 to ensure quality and compliance.
Selecting the right steel pipe and purchasing it
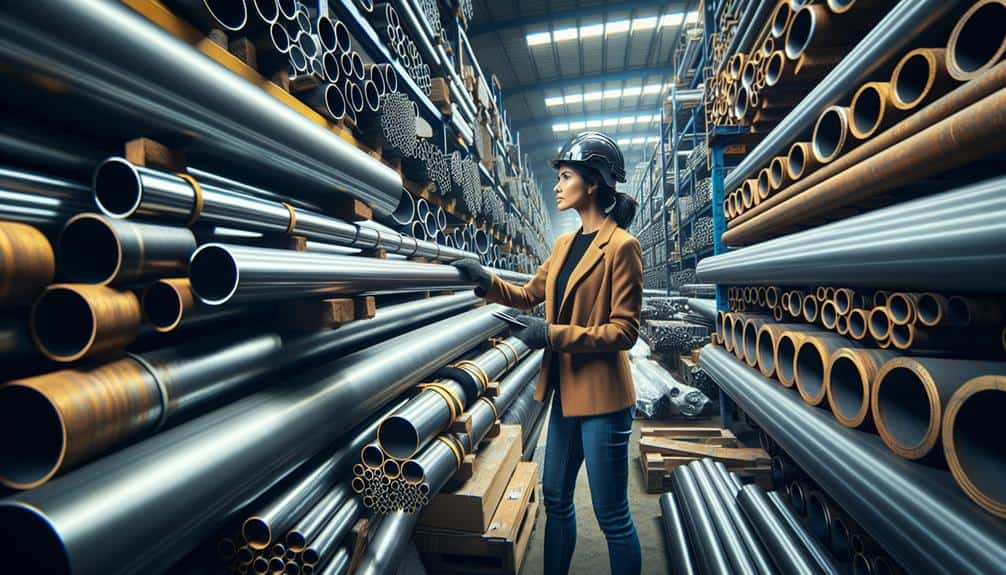
Obtaining the suitable steel pipe requires a thorough evaluation of material composition, size specifications, end connections, and adherence to industry standards and certifications.
When selecting a steel pipe, it is important to ponder the intended application to determine the most suitable material composition. Factors such as corrosion resistance, strength, and ductility play a significant role in this decision-making process.
Size specifications must align with the requirements of the project, taking into account both diameter and wall thickness to guarantee structural integrity and efficient fluid flow.
End connections are essential aspects to assess when choosing a steel pipe, as they determine how the pipe will be joined to other components or structures. Common connection types include threaded, welded, and flanged ends, each suitable for different applications.
Additionally, verifying that the chosen steel pipe meets relevant industry standards and certifications is crucial. Compliance with standards such as ASTM, ASME, and API ensures the quality and performance of the steel pipe.
Frequently Asked Questions
Can Steel Pipes Be Used for Underground Installations?
Steel pipes are commonly used for underground installations due to their durability, strength, and resistance to corrosion. Proper coating and installation techniques are crucial to guarantee longevity and prevent damage in underground applications.
Are There Any Environmental Considerations When Choosing Steel Pipes for a Project?
When picking steel pipes for a project, it’s important to take into account environmental factors. With steel boasting a recycling rate of over 90%, it stands as a sustainable choice. Additionally, coating options can improve corrosion resistance, extending longevity.
What Are the Advantages of Using Seamless Steel Pipes Over Welded Ones?
Seamless steel pipes offer superior strength, uniformity, and reliability due to their uninterrupted grain structure. They are resistant to corrosion, pressure, and temperature variations, making them ideal for high-pressure applications in industries such as oil and gas, automotive, and construction.
Can Steel Pipes Be Recycled After Their Lifespan?
Steel pipes can be recycled after their lifespan. The recycling process involves collecting used steel pipes, melting them down, and reshaping the material into new steel products. Recycling steel pipes helps conserve resources and reduce environmental impact.
Are There Any Specific Safety Measures to Consider When Working With Steel Pipes?
When handling steel pipes, it is essential to adhere to stringent safety protocols due to the inherent risks associated with their weight, sharp edges, and potential for high-pressure contents. Protective gear and proper training are imperative.
Conclusion
To sum up, steel pipes are vital components in various industries due to their durability and versatility.
One interesting statistic to note is that the global steel pipe market is projected to reach $68.4 billion by 2026, with a CAGR of 3.6% from 2021 to 2026.
Understanding the types, processes, and options available for steel pipes is essential for making informed decisions in selecting and purchasing the right steel pipe for specific applications.